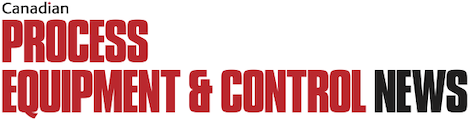
Case Study: Self-cleaning filter for calcium sulfonate grease increases productivity and reduces costs
Mike Edwards
Features Eaton John Brooks Company
A global manufacturer of specialty chemicals traditionally employed manual filtration to filter calcium sulfonate grease. This manual process used bag housings and polyester multifilament bags rated at 600um.
This process required frequent filter change-out resulting in high maintenance and downtime and a high degree of filter bag disposal. Additionally, on occasion where bags couldn’t handle the high backpressure, they would get damaged, causing dirty products to bypass the filtration housing and damaging equipment downstream — affecting productivity and product quality.
THE SOLUTION
An application expert at John Brooks Company consulted with the customer to upgrade the filtration equipment at the facility. The manufacturer ultimately selected the Eaton self-cleaning DCF 1600 filter as the solution for their application.
During the consultation process, it also came to the expert’s attention that the grease was highly viscous, and it took a long time to pass through 2 in. pipe and into the housing. John Brooks changed the piping from 2- to a 3-inch connection for faster operation and offered the DCF-1600 rental unit to the customer on a trial basis.
During the trial, a plugging issue occurred. During production, the grease would start to cool down and thicken, making it harder to filter, clean and purge. A steam jacketed housing was selected to prevent the grease from thickening. Once installed, the customer noticed they were getting a much cleaner final product downstream, and the self-cleaning filter was effortless to maintain. The DCF could handle backpressure better than the bag housing, and the customer didn’t have to worry about buying and disposing of bags anymore.
THE RESULTS
- Increased Productivity & Efficiency
- Decreased Downtime
- Reduced Labour & Maintenance
- Increased Product Quality
HOW SELF-CLEANING FILTERS WORK
The process begins as the unfiltered fluid enters the inlet of the cylindrical stainless-steel housing unit containing the filter screen. As the liquid passes through the filter, the screen catches the solids floating in the fluid and keeps them inside the housing unit while the fluid exits the outlet.
The screen inside the housing requires cleaning to continue to filter optimally. The DCF 1600 has a unique spring-loaded cleaning disc that moves up and down the housing, cleaning the media and concentrated solids in both strokes.
Once the slotted screen is cleared of debris, the cleaning disc directs the contaminants to the bottom of the housing and out of the flow path. This cleaning process happens while the filter remains in service, thereby maintaining the efficiency of the process and reducing the loss of valuable product.
Because of the unique temperature requirements for this application, a steam jacketed (SJ) housing was used for the filter. SJ housings are best used for applications where the fluid must be kept hot to remain fluid, e.g., applications like chocolate, asphalt, resins, and polymers. The housing body maintains the fluid’s temperature by circulating steam or a heat transfer fluid through the jacket on the housing, handling steampressure up to 100 psi.
This application story was contributed by John Brooks Company.
Print this page