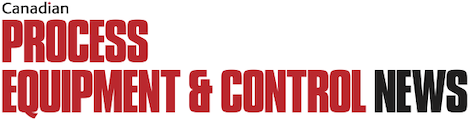
Moisture measurement & control for product quality from lab to line
Mike Edwards
Features control IR-3000 Online Moisture Sensor MoistTech NIR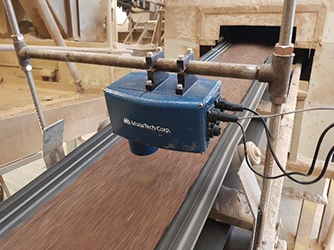
What is worse than wasted effort? Economical losses and decreased productivity. Moisture measurement is a crucial aspect in manufacturing from the initial process to the end-product stage.
Product quality and consistency are forefront with MoistTech in the development of its IR3000 sensor to accurately provide moisture and coating measurements throughout the process, yielding a consistent product quality from lab to line that immediately reduces down-time, wasted energy and product loss.
Your product should be top quality every time it leaves the facility and measuring the amount of moisture can be a crucial step in the process, too much or too little can be detrimental to the overall product. The technology behind MoistTech’s design is what provides precision results: Near-Infrared spectroscopy and imaging.
NIR utilizes a fast and nondestructive analytical technique that provides chemical and physical information of virtually any matrix. Using light absorption, NIR analysis can give accuracy results of ±0.01%. Non-contact online sensors with hundreds of measurements per second are transmitted to a PLC which allows line personnel to make immediate line adjustments if necessary. The no-drift optical design requires no maintenance, is insensitive to material variations such as particle size, material height & color, requires a one-time calibration and provides continuous reliable readings.
Measuring and controlling moisture can reduce transportation costs due to shipping excess water and moisture control stops products from freezing during shipping and transportation. Testing moisture content throughout the process also provides manufacturers cost savings in energy & fuel costs, as well as having less product waste. With continuous NIR online moisture testing, manufacturers can monitor moisture levels which they in-turn, can precisely control their dryers to optimize the production process with minimum energy requirements. Reduce downtime, start-up time, waste and energy costs by monitoring the moisture levels at every stage of the process. When one measurement is out of tolerance, a quick automatic or manual adjustment can be made to keep things moving correctly before costly time is lost, and waste is produced.
In addition to moisture measurement, MoistTech’s technology has the ability to measure and monitor fat, oil, coating moisture and thickness applications, making it the gold standard in quality control in virtually any manufacturing process.
Moisture measurement is critical in all aspects of the materials process; thus, manufacturing companies are constantly adjusting moisture to maintain the quality of their product. Advances in real-time sensing, data collection, and data analysis & interpretation helps to determine the characteristics of the materials prior to processing, providing process efficiency and optimization. Regular measurements of moisture remain a necessity for control of drying, thereby reducing treatment costs. Additionally, small variations and excess moisture in mixes can result in clumping affecting quality and consistencies in mineral and other similar materials; too dry of a product can result in excess dust. Measuring moisture in applications prior to crushing can control particle size and provide dust suppression. During the drying stage, in-process measurements ensure optimization and elimination of over drying, which can lead to product that is out of specification, degradation and an excess of dust.
Designed to provide accuracy and repeatability, the MoistTech NIR technology is a ratio-based measurement with prime beam; this eliminates the sensitivity to distance, improves stability and accuracy and provides a no drift design. Engineers created algorithms, wavelengths, and sensor optical requirements to take thousands of detailed, accurate measurements per second. The ability to pre-set the measurement rate to match the production rate is available on the technology and because there are no routine re-calibrations, this technology is low to zero maintenance, making it an ideal solution for the manufacturing process. With the ability to store up to 50 product/calibration codes, line personnel can alert the sensor for changing products immediately. The technology also has the ability to measure up to 3 constituents in a product at once including: moisture, coating/thickness, and temperature.
Net result: Improved quality and reduced production costs by savings in energy and loss reduction.
- Product Quality Monitoring
Allows immediate production line adjustments to improve product quality and consistency.
- Process Optimization
Allows 100% monitoring of your production process to reduce product that is “out of specification”
- Fuel Consumption Savings
Reduce your energy usage as the drying/cooking process can be controlled resulting in a reduction in energy consumption.
- Water Savings
Reduce your water usage by continuously monitoring moisture content
- Dust / Fire Prevention
Helps reduce the risk of explosions due to dust
The addition of the MoistTech IR3000s have provided one customer with the ability to control its process by instantly increasing or decreasing the material flow into the dryer. This variation of its material flow is based on the moisture content and belt scales to provide a dry weight. Prior to the MoistTech technology proved to be a guessing game and time-consuming OWL laboratory tests post dryer.
For the last few years the company integrated the MoistTech Online Sensor into its customer’s scopes with the goal of a fully optimized closed loop control. When integrated with its stacker, it reclaimed lower operating costs, safer storage and improved product quality. The instant feedback informs our plant personnel of controlled moisture all throughout the entire process.
Before the MoistTech IR-3000 Online Moisture Sensor was installed, the only method of measurement was by grabbing a sample and taking it to the lab. The customer’s lab method consists of weighting the sample, drying at a low temperature for a certain amount of time and then weighting it again, based on the lost weight they calculate the amount of moisture of the product. Unfortunately, this method takes a lot of time and if the product is running out of the moisture range needed then by the time the company figured out the moisture content is too late and this represent loss of energy and product that needs to be reclaimed.
By installing the MoistTech IR-3000 Online Moisture sensor over the process, its customer could now monitor the moisture continuously at a ±0.1% accuracy which helped tremendously with being able to make any adjustments on the speed or the temperature of their dryers. The sensor was also integrated with their PLC using one of three 4-20mA outputs.
Not only can the IR-3000 measure moisture but also the customer applies a water-based coating to some of their product and the sensor can measure the thickness of the coating at a very successful accuracy. Installing the IR-3000 Online Sensor will help the customer act immediately on any issues that might arise during production.
The system is working very well with an efficiency improvement of 400-600 % improvement in moisture control. MoistTech is also looking at promoting this to a best practice suitable for our other plants and shingle lines.
A moisture sensor should be installed in several locations throughout the process including screw conveyors, belt installations, pipeline or pneumatic conveying, cyclones, chutes, bins, and exits of dryers or final stages of manufacturing. Generally, moisture control sensors are located in the most critical stages of the process however the location is often determined by the space available as well as the manufacturers requirements. This technology can be implemented as a standalone sensor for single point measurement or positioned on a cross profiling measurement system. Installation 4 to 16 in. above the product to continuously monitor the process and control the moisture content will yield the best results.
This white paper was provided by MoistTech of Sarasota, FL, which covers North & South America, and other locations across Asia, Africa, the Middle East and Europe.
Print this page