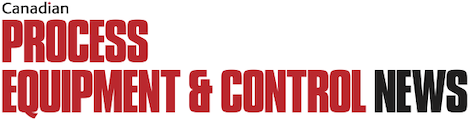
The choice of structural material for enclosures that protect outdoor equipment in industrial process applications is key to long lifecycle performance, especially in extreme environments. However, engineers tasked with making this choice often face a multitude of conflicting demands. The protective enclosure must provide adequate protection against extremes of cold and/or heat, but will often also need to be resistant to many other risks. These can include driving rain or snow, high wind speeds, corrosive media and intense UV.
Depending on the application, the enclosure may also need to be capable of withstanding pressure blasts, explosions or fire. A key underlying requirement will invariably be that it should combine robust structural integrity with a long service life – and need little or no maintenance.
Steel enclosures have long been a popular choice for equipment containment. However, although perfectly suited to indoor use, they are often less than ideal for outdoor field-based applications. Even galvanized steel is highly susceptible to corrosion, especially in coastal or offshore locations, and requires regular repainting. Another major disadvantage of steel is its high thermal conductivity (typically 15 – 50 watts per meter kelvin), which makes it difficult to insulate.
Simply adding layers of internal insulation to a steel enclosure is rarely adequate, because any metal tubing or cables passing through its walls – and there are always some – can introduce serious ‘thermal short cuts’. These effectively couple the inside of the enclosure to its highly dissipative exterior surface. It is not unusual for such thermal short cuts to account for as much as 80% of the energy losses in a heated enclosure, which can have a major impact on the size of heater that needs to be fitted, and on operational costs.
Many manufacturers produce enclosures for instruments from plastic materials such as polycarbonate (PC), polystyrene (PS) and acrylnitrile-butadiene-styrene (ABS), but there is no ‘one type suits all’ solution. Enclosures made from PS or ABS are not always suitable for protecting field-based equipment, because they degrade over time when exposed to UV. And while PC does offer excellent resistance to UV, and to impact damage, it is susceptible to stress cracking and chemical attack. If the installation environment is prone to extremely low temperatures – something that is becoming more common today – thermoplastic enclosures can become very brittle. GRP remains stable even down to -100 degrees C.
Optimum material properties
Another material possibility for outdoor protective enclosures is glass reinforced polyester (GRP). Although GRP is a little more expensive to manufacture than plastic, it offers many unique advantages. These include excellent insulating properties (GRP sheet material has a much higher thermal resistance than metal and can easily be made with perfectly bonded insulation that is ‘embedded’ within the structure and conforms exactly to its shape).
Other advantages include immunity to corrosion from salt and gases such as hydrogen sulfide (H2S), sulfur dioxide (SO2) or carbon dioxide (CO2), rigidity, and a very wide operating temperature range. GRP is also resistant to most petrochemicals, including benzene, butylene, ethylene, napthalene, propylene, toluene and xylene.
The company that I work for, Intertec, uses GRP as the basis for all its protective enclosures, cabinets and shelters. The fabrication process depends on the type and size of enclosure – sheet molded compound (SMC) is mainly used for instrumentation enclosures, while various combinations of resin transfer molding (RTM), continuously made sheeting, pultrusion or hand lamination are used for larger cabinets and shelters. GRP is about 100 times more stable than non-reinforced plastic and it has a similar strength to stainless steel, but weighs 75% less.
The very low thermal conductivity (approximately 0.2 watts per meter Kelvin) of GRP makes it an ideal building material for protective enclosures intended for use in severe environments. The walls of many of Intertec’s enclosures are made from a composite version of this material, with inner and outer GRP layers ‘sandwiching’ an internal core of closed-cell polyurethane (PU) foam. The thickness is chosen to suit the specific application and the severity of the environment, and is typically between 20 and 100 mm.
Proven long-term performance
Intertec has produced more than a million GRP-based protective outdoor housings, many of which are installed in severe environments. For example, the company supplied nearly all the instrumentation enclosures for the large Irving Oil refinery in Saint John, New Brunswick. Most of these have been in service for at least 30 years, but show little evidence of ageing, other than a slight roughening of surface finish (often referred to as ‘chalking’ or ‘frosting’). This is despite an extremely hostile environment combining salt air with very cold winters, hot summers and temperatures that can change very rapidly – and by several orders of magnitude in a single day during the spring.
For process plant applications, two of Intertec’s most popular designs are its MULTIBOX and diagonally opening DIABOX ranges of protective enclosures. Offering a wide choice of containment capacities from 25 to 277 liters, these feature a two-part construction for ease of instrumentation installation and maintenance access. For applications that require protection against extremely cold climates, the enclosures are available in ‘arctic’ configurations that are suitable for use in temperatures as low as minus 60 degrees Celsius.
MULTIBOX and DIABOX enclosures are widely used for offshore as well as land-based applications. One recent project for example involved supplying DIABOX enclosures ready-equipped with the necessary tubing, valves and process transmitters, for a gas field in the Atlantic, off the coast of Nova Scotia. Each enclosure is also fitted with an explosion-proof heater and sealed thermostat, for freeze protection. The enclosures were chosen primarily because they have the strength and corrosion resistance needed for the site’s harsh operating conditions, combined with the low weight that is desirable for offshore rig installation.
Intertec is also supplying protective enclosures for many of the other severe climate applications that can be found in North America. These include projects on the Alaskan North Slope – some 250 miles north of the Arctic Circle – and in the Alberta oil sands.
The popularity of GRP instrumentation enclosures has now led Intertec to extend both product ranges with Type 4X versions.
Ted Zavitz
Technical Director – North America, Intertec Instrumentation
www.intertec.info
Print this page