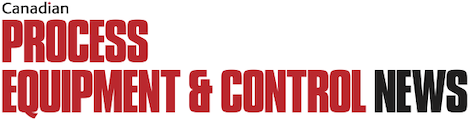
As the saying goes, when the only tool you have is a hammer, it doesn’t take long for every challenge to start looking like a nail. It may sound like heresy coming from someone who makes his living in the filtration industry, but a filter is not the answer to every contamination problem. In fact, there frequently are better, less expensive solutions that may be overlooked when system designers focus exclusively on filtration.
What I’m talking about, of course, is a strainer which is often the ideal solution for cooling water applications that don’t really need fine filtration. Where their use is appropriate, strainers offer a number of advantages over filters. These include lower initial investment, much lower maintenance cost, and service life measured in decades rather than weeks or months.
Installing an automatic self-cleaning strainer in an HVAC cooling water system, for example, can protect heat exchangers, pumps, valves and spray nozzles, while continuously removing entrained solids and providing continuous flow – even while the system is being backwashed. When properly sized and configured, such a system literally can operate for years, or even decades, with little or no maintenance required.
The strainer system protecting an HVAC cooling tower water supply in a major international airport is a good example of the effectiveness of this technology. The passengers and employees are served by a heating, ventilation and air conditioning plant with a single cooling tower located in the central terminal area. It operates 24 hours a day seven days a week under all weather conditions.
At full load, the tower circulates 25,000 gallons per minute (gpm) of water. Because of space constraints, the strainers protecting the tower and associated equipment also are the primary source for removing dirt and other impurities from the entire system.
The open cooling tower collects a wide variety of contaminants from road dust and pipe scale to seasonal leaves and even the occasional branch during stormy weather. Anything larger than 0.062” (1.6 mm) is removed by the strainer producing discharge water clean to 200 parts per million (ppm). That figure may not sound very impressive until one does the calculations. A system flowing 25,000 gpm and removing an average of 1.9 pounds of contamination per 1,000 gallons removes about 9.5 tons of waste from the cooling water stream per day.
The strainer is a 36-inch fabricated automatic backwashing self-cleaning unit. The carbon steel housing is 78” in diameter and 148” high (198 cm x 376 cm) with a corrosion-resistant coating and a maintenance-free, non-leaking proprietary double mechanical Viton® seal.
All of the moving components of the system are attached to the cover, so if the unit ever does need to be opened for maintenance no further disassembly is required. This design produces a unit that is essentially a giant cartridge-type filter, but one that does not require periodic replacement of the element.
The strainer element is a proprietary Dura-Wedge™ screen constructed of V-shaped profile wire. The element provides two-point contact straining from the “smooth” side that prevents plugging or packing of debris and particles. It also provides effective dislodging of collected debris during the backwash cycle.
The strainer design minimizes fiber stapling, and vertical collector bars are included to prevent snow plowing of materials by the rotating backwash arm and port shoe. The all-welded design includes circumferential reinforcing bands to enhance structural integrity in the completely sealed element.
The automatic control system continuously monitors the strainer and initiates a backwash cycle when flow restriction reaches a pre-determined level. A high-efficiency rotating backwash arm extends the entire length of the screen, isolating the portion it contacts. When the backwash arm is vented to atmospheric pressure via the backwash valve the flow through the screen reverses and the debris collected in the area under the backwash arm flows out of the strainer.
Since most of the screen area continues to strain, backwashing is accomplished without interrupting the flow of cooling water. Only a small amount of strained liquid is used to carry away and dispose of the debris.
The system has been in continuous use for more than 15 years without maintenance or attention, which clearly demonstrates the durability of a properly designed strainer system. It is periodically pressure tested to meet ASME code requirements, and although it is approaching the end of its 25-year design life there is no indication it will need to be taken out of service anytime soon.
Strainers are widely used in many industries for applications where particles no smaller than 50 microns have to be removed from a cooling water stream. In general, a strainer is often the best choice for cooling water in non-critical applications where 50 micron or smaller contaminants will not adversely impact the process or equipment.
Most manufacturers offer both standard and fabricated strainers suitable for use with either fresh or salt water. Available materials include carbon steel, various grades of stainless steel, copper nickel, monel, aluminum/bronze and other, more exotic materials for special applications. Corrosion-resistant coatings, including epoxy paints, are frequently used for internal components of carbon steel strainers for fresh water applications.
While a strainer is often a cost-effective alternative to a filter, it’s also a worthwhile addition to a filtration system. Filter life can be significantly extended by using a strainer to remove large contaminants before they reach the filter element. In many cases, the strainer will more than pay for itself in terms of filter element savings alone, not to mention the reduction in downtime and maintenance costs incurred in maintaining a filter system.
Whether the solution for your system is a high-performance filter, a durable, maintenance-free strainer or both, investing the effort to explore the full range of options is well worth the effort. Selecting the right solution will pay dividends for many years to come.
by Anthony Chiang, Eaton Technical Sales Specialist
www.eaton.com/filtration
Print this page