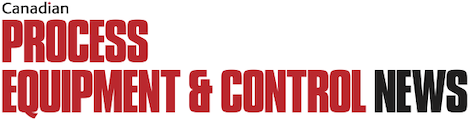
By Victor Outrebon / Endress+Hauser Canada Ltd
Historically, industrial process measurement and automation manufacturers have been constantly improving the performance of instruments to reach a better accuracy and repeatability or to ensure safer operations in the field.
In the meantime, demand has steadily grown for simple, reliable and maintenance-free measuring instruments with compact designs. Manufacturers have had to adapt to new requirements from the process industry. Contrary to highly sensitive measurements where performance, accuracy and safety are critical, utilities and secondary circuits measurement are also valuable but require rather simple, compact and cost-efficient devices. Over the last few years, instrumentation manufacturers have expanded their offering of user-friendly and basic devices to adapt to that new demand.
Simplicity in the field
With ever improving performance and functionality, instruments in the field could appear to require an increasing level of time and knowledge for their selection, sizing and commissioning. Staff training could also be an issue with continuously evolving software and device maintenance.
Simplicity of operation is important for basic functionality sensors. These additional sensors in the field should be almost installed and run autonomously to keep the focus on major production lines. Therefore, simplicity of installation and minimal maintenance are key for these types of cost efficient instruments.
Integration of utility circuits in Industry 4.0
In the context of Industry 4.0, sensors and control systems are becoming the ears and heartbeat of processes across all industries. Advancements in digital protocol in process automation are also allowing a smoother implementation of these basic measuring instruments in the field.
With most companies having set up energy reduction programs focusing on efficiency, major plant operations and utilities can be monitored on the same level. Capturing and optimizing utility operations not only provides better system visibility but also contributes to better productivity in the field.
Examples can be found in all industries, not only for utilities. Monitoring the flow of secondary circuits such as heating or cooling lines is beneficial for optimizing productivity in the field. In the primary and metals industry, industrial furnaces can have a substantial number of return lines where temperature and flow need to be monitored. Due to space restrictions and cost of traditional instruments, compact flowmeters do now allow monitoring of these cooling lines to detect leakage at a reasonable cost.
In the food and beverage industry, cleaning and rinsing applications could be quite costly due to the amount of water they require. Monitoring process water or controlling water consumption in cooling processes could help reducing the utilities bill and impact the bottom line significantly.
Water, Air, Gas, Energy and Steam (WAGES) in the field can now be fully monitored. As the processes move towards Industry 4.0, their integration into a digitalized process environment is also to be considered.
Digitalization for all instruments
A seamless integration of these basic devices is necessary in a digital environment. Quite often, these entry-level instruments are not considered because of their lack of compatibility with the rest of the instrumentation in the field moving towards digital protocols. For a long time, instrumentation manufacturers have refrained from implementing digital communication into their basic sensors, for cost optimization.
Developed by a consortium of industrial manufacturing companies, IO-Link is a digital protocol that offers improvements in the implementation of basic sensors in the field. Time and cost of project implementation can be reduced significantly thanks to this open protocol. It is a point-to-point technology that enables access to diagnostics and tracking capabilities from sensors and actuators. Each IO-Link device is connected to an IO-Link master, that acts as a gateway to a field bus such as Ethernet/IP. Since IO-Link is not a Fieldbus dependent system, it can be added to existing control systems at minimum cost.
Other advantages of IO-Link technology include the automatic transfer of parameters after device replacement as well as less wiring as compared to conventional wiring.
In some confined spaces where direct wired communication could be critical, some instruments feature wireless communication capabilities such as Bluetooth. This allows commissioning of devices as well as reading process values and accessing diagnostic information remotely. Manufacturers such as Endress+Hauser have implemented Bluetooth capabilities into flow or level sensors, accessible via smartphones via an app.
Plug-and-play flowmeters for utilities
Flowmeters represent a vast share of instrumentation cost in the field across all industries. Due to their high accuracy and advanced functionality, process automation professionals tend to install them on process critical lines only, mainly because of their high price point. Utility flows (monitoring of cooling lines or process water for instance) often don’t get measured even though they could bring significant information to field operation personnel.
Smart plug-and-play flowmeters that measure and monitor flow and temperature of conductive liquids can be cost-efficient. In addition to their high-accuracy flow sensors, Endress+Hauser has developed a compact flow meter with intuitive operation thanks to a wide display, offering Bluetooth and IO-Link compatibility.
The Picomag combines a sensor and transmitter in the same housing, with a 1.4″ TFT colour display showing flow, totalizer and temperature readings, as well as warning and alarm messages. Outputs include 4-20mA, pulse, switch and 2-10V. The Bluetooth wireless interface allows direct access to process and diagnostics data, and enables the user to configure the measuring device on the fly. The device can be operated and configured on Android and iOS devices via the free SmartBlue App available for Android and iOS. It is possible to carry out wireless configuration or data retrieval over a distance of 10 meters – even at installation sites which are difficult to access.
Errors occurring during operations are displayed via diagnostic symbols in accordance with NAMUR recommendation NE 107 (same standardized message as per the high-end flow instruments available in the market). The screen rotates automatically depending on the installation position, guaranteeing optimal readability at any time. Configuration parameters can be called up and monitored by simply knocking on the device.
Due to its compact design, Picomag can be installed flawlessly into any pipe up to 50 millimeters (2″) in diameter, even in confined spaces. For this purpose, there are various process connection adapters available, such as NPT-thread, R-thread, internal thread, Tri-Clamp or Victaulic. Picomag is a cost-optimized solution for applications where the focus is on high repeatability (±0.2% o.f.s.). Picomag is suitable for process temperatures between –10 to 70 °C (14 to 158 °F) as well as for process pressures up to 16 bar (232 psi). The robust Picomag housing made of stainless steel (IP65/67) is available in two designs.
With a whole new segment of basic functionality instruments, all industries can now access cost-efficient instrumentation to complement their advanced sensors in the field.
Print this page