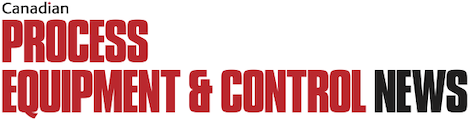
By Kristina Urquhart / Manufacturing Automation
The CEO of ATS Automation says he “couldn’t be more proud” of his workforce as the company pivots to produce medical devices at its facilities, and ramps up production of equipment needed by other manufacturers during the COVID-19 crisis.
On Apr. 14, ATS, which operates 23 manufacturing sites globally and is headquartered in Cambridge, Ont., announced that it had signed on for contract manufacturing for critical medical equipment needed for coronavirus treatment at its locations in Cambridge and Chicago.
CEO Andrew Hider says that assembling ventilators was an easy switch for the company, since 55 per cent of its business already lies in building automated equipment for life sciences manufacturing.
“We understand all of the certifications and dynamics that must be met,” he says. “Fortunately, our supply chain leader has been out in front in ensuring that our supply chain is low risk, and we’ve been able to maintain that.”
ATS’s experience in a sector that has critical customer need means the company was poised to handle requests for equipment needed to fight coronavirus, Hider says.
“We’re [already] providing many of the solutions that people’s lives daily depend on. And our customers won’t accept that they can’t continue to produce – whether you’re using an inhaler or an injectable, you can’t not get that product.”
That capability is also what’s allowing ATS to focus on what it does best – engineering, designing and building the machinery and equipment needed by other manufacturers to scale up their operations or retool to produce medical devices and personal protective equipment (PPE).
‘Rinse and repeat’ production
Hider says the ATS’s biggest strength is in helping companies scale from prototype to full-scale production, which it does through machine building for automated systems.
“Once you’ve identified the product and you have the final solution, it’s that rinse and repeat,” Hider says. “You continue to build out your production process.”
Out of its Chicago location, ATS is supplying two manufacturers with equipment that calibrates and tests ventilators before they are distributed to medical facilities. The company has also delivered equipment for production of filtering facepiece respirators to a large automaker.
In Canada, ATS is working with O-Two Medical Technologies to assemble ventilator components at its facilities. The components are being produced in collaboration with automotive parts manufacturers Magna International, Martinrea International and Linamar Corp.
To get the assembly project started, the ATS technology team met with O-Two over the course of a day to understand their needs for the ventilators and how they would ramp up the project. Hider says a need for speed and quality were at the forefront.
The ventilator assembly project will run for about two months.
In a separate project, ATS has also manufactured a prototype machine that could potentially help to treat COVID-19 symptoms. The device has not yet been approved for use.
The tool and die maker builds tooling, and does CNC machining, design and fabrication for the automotive and nuclear sectors, as well as for automation companies such as ATS and Eclipse Automation.
The prototype parts “are complex, there’s tooling required that we’ve had to kind of makeshift in the short term – but it’s nothing that we haven’t done in the past,” says Chris Hergott, vice-president operations and owner of XL Tool.
Hergott says that since the pandemic started, he’s had to lay off 10 non-essential workers in an effort to ensure physical distancing in the shop. Breaks are staggered, and staff are reminded to stay two metres apart.
“For the most part, people want to work,” he says. “They don’t want to be at home, they don’t want to be out of work.”
Hergott is also president of the Canadian Tooling & Machining Association and says he is in talks several times a week with members about how they are handling the impact of COVID-19.
“This thing is going to drag on for a while. How is business going to change? Are people going keep traveling?” he says. “More stuff could be made at home [in Canada], so we’re trying to look objectively at what could or will be the future for any manufacturing industry.
“The more we talk, the better.”
‘A new game’
Hider says keeping the lines of communication with customers open during pandemic has been crucial for ATS.
In the absence of conducting in-person service visits, the company set up a remote, virtual support system called Live Coach within five days of the government’s orders to halt travelling. With the platform, customers are able to get engineering support and feedback via a live stream.
Hider says the company will continue to use Live Coach after the pandemic. “It’s just another option that we can help our customers maximize their performance regardless of where they are.
“We said, okay, here’s the new game. How do we plan, how do we win? Winning is protecting our people, and ensuring our customers can get their product to market.”
Print this page