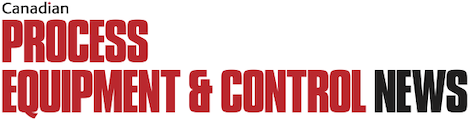
The world saw the emergence of peristaltic pumping technology in the in 1930s. In those early days peristaltic pumps were severely limited due to the limitations of rubber technology. Rubber technology has continued to advance over the past 85 years. Even in the past 25 years we have experienced remarkable advancements in automobile tire performance and lifetimes. Due to advancements in rubber capabilities and peristaltic pump design the peristaltic pump category is the fastest growing segment in positive displacement pumps.
Some of the unique capabilities of peristaltic pumps are their ability to run dry without damaging the pump, the ability to suction lift materials, the ability to handle highly corrosive mediums and finally the ability to handle abrasive very high solid content slurries up to 80% and beyond. The fact that these pumps do not require gland seal water as well is a desirable attribute too. But not only not requiring gland seal water these pumps can help to save immense amounts of water. For instance in some mining regions water is not abundant and even it is it has a significant cost.
If you can pump 80% solids with a peristaltic pump you can reduce the overall total gallons per minute and in some cases downsize other machinery, valves and piping. For instance to move 35% solids with a centrifugal pump you would require 65% make-up water. With the peristaltic at 80% solids you would only require 20% make-up water. The total flow going through the piping and entire system would be about ½ the amount by using the peristaltic pump. Also pumping higher solid content slurries to filtration systems may also enable to the user to improve efficiency of the filter and improve overall throughput of the operation. Less time in filtration improves production and reduces energy costs.
As mentioned before, the rubber advancements have made significant contributions to the usefulness and reliability of peristaltic pumps. There have been some recent advancements in the design of peristaltic pumps that again increase the usefulness and reliability even further. Dating back to the 1930 the first peristaltic pumps operated on the principal of a fixed rotation point and two shoes that rub against the hose to compress the rubber hose. The rubbing action requires this type of pump to utilize large quantities of glycerin in the pump housing. The glycerin is used to provide lubrication but more importantly it is used to dissipate heat.
In many designs the pump housing is filled up to 1/3 or even ½ of the pump housing with glycerin. If the pump is a 2.5” or 65mm then the amount of glycerin may be 5 gallons or more. This glycerin costs around $100 per gallon and once the sleeve breaks the glycerin has to be disposed of. Then a new hose is installed and another $500 of glycerin. Two shoes compress the rubber hose twice every 360 degree revolution. Since the number one factor that contributes the most to hose life is the number of times you compress the rubber hose then if you can eliminate one of those compressions per revolution then will likely double your hose life.
There are also two roller peristaltic pumps but they also compress the rubber hose twice per revolution. I mentioned that the shoe designs generate a significant amount of heat. For this reason the rotational speed of shoe designs needs to be limited. They often have a pump curve that includes a continuous duty box and an intermittent service area. This is because as the revolutions per minute increases then so does the temperature of the pump. This temperature also has a detrimental effect to the hose lifetime as well.
In the past 10 years there are new designs on the market that incorporate an eccentric shaft and a single roller to compress the rubber hose. The advantage is tremendous for the end user. First of all the hose lifetime increases substantially when compared to shoe designs. The typical improvement is 3 – 5 times longer for a single roller design compared to shoe designs and multiple roller designs. Also the pump generates virtually no heat build-up so there is no need for large amounts of glycerin in the pump housing. For instance a similar 2.5” or 65mm pump will require only ½ gallon of glycerin for light lubrication of the hose compared to 5 gallons required in the shoe designs.
Again because the pump does not generate heat it does not have a continuous duty and intermittent duty box. It only has a continuous duty curve. So the pump can be run at much higher revolutions per minute and still produce tremendously longer hose lifetimes. In most cases you can use one size smaller pump per flow rate to achieve the same flow as you could with the shoe design. Finally the energy consumption of a rolling design is less than a shoe design saving the user additional cost. The net result to the user is that a rolling design saves anywhere from 40 – 70% additional operating costs compared to dual shoe or dual roller designs. In a large number of cases particularly with larger diameter pumps the operational cost savings by using a single roller design will generate enough savings that you will be able to purchase a new pump every 1 – 1.5 years to replace the high operational cost dual shoe designs.
www.flowrox.com
Print this page