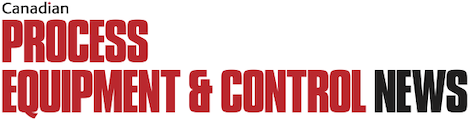
Frost & Sullivan’s recent analysis of the adoption of digital technologies and smart devices in the global industrial equipment market finds that the convergence of information technology (IT) and operational technology (OT) is rapidly transforming the industry landscape and providing actionable intelligence to decision-makers.
The Internet of Things (IoT), big data analytics, sensorization, artificial intelligence (AI), and machine learning (ML) are ushering changes in various industries, including oil and gas, mining, chemicals, food and beverages, power, and water and wastewater.
Global revenue for digital technologies in the industrial equipment market is estimated to reach US$4.19 billion by 2027 from US$1.5 billion in 2020 at a 15.8 per cent CAGR. The Americas lead industrial equipment innovation, with many digital solution providers headquartered in North America. The region will attain $1.7 billion in revenues by 2027, followed by Europe, the Middle East and Africa (EMEA), and Asia-Pacific (APAC).
The water and wastewater sector is expected to top investments in digital solutions with US$2.2 billion by 2027, followed by the chemicals industry with US$667.6 million.
“Rapid urbanization and the explosive rise in water consumption make efficient water management systems critical,” said Anand Gnanamoorthy, Industry Principal, Industrial Practice at Frost & Sullivan in a statement. “Water enterprises and government bodies are pushing for modernization of water infrastructure by using IIoT-based technologies that help ensure zero wastage and unplanned plant maintenance. This has led to a surge in demand for asset monitoring solutions, including pumps, compressors, and mixers used in fundamental processes.”
Gnanamoorthy adds that “Access to low-cost feedstock from shale reserves is also expected to fuel investments in the chemical industry to meet global demand. End users want to monitor their plant but do not want the data to be stored/shared beyond the plant due to concerns of loss of intellectual property (IP). The need to avoid unexpected asset downtime and production delays caused by a dependency on manual inspection is likely to promote the use of component monitoring solutions that allow data sharing only within the plant.”
To increase growth opportunities, stakeholders should explore these strategic recommendations:
- Focus on IIoT-based solutions for overall plant performance management: Creating solid prognostics capabilities through partnerships with IIoT solution providers will help them consolidate, analyze, and interpret data, reducing the total cost of ownership throughout the plant.
- Deploy IIoT solutions to disrupt business models for end users across industries: Original equipment manufacturers (OEMs) should invest in IIoT-based technologies such as cloud computing, edge analytics, AI, and blockchain to offer high-caliber, dependable, and comprehensive services to clients.
- Ensure quality control management for improved plant productivity: As end users understand the importance of quality control and strive to deploy the latest quality control management systems, industrial equipment manufacturers should sensorize and enable their equipment to collect, process, and analyze operating data used in these solutions.
- Emphasize the connected distribution network for better maintenance: OEMs should build a unified platform with IIoT and work with channel partners to offer a top-tier service experience for tracking equipment and parts and expediting delivery time.
Print this page