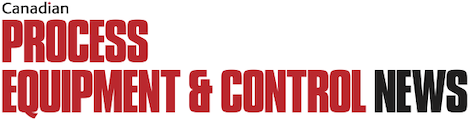
Learning from human error: How BP’s Human Performance Framework is improving site safety
Don Horne
Process West features pw featureIn the lead up to the Operational Excellence in Energy, Chemicals & Resources Summit, we sat down with Hugo Ashkar, global risk manager at BP, to discuss his work in human performance and the role of human factors in overall risk management.
Hugo, can you tell us about your role as Global Risk Manager at BP?

Hugo Ashkar
I lead the execution of risk management activities in BP’s global portfolio of major upstream construction projects, both on-shore and off-shore. Ours is the largest projects organization in BP, and we currently have 60-75 projects and any given time, all of which are considered major projects in terms of complexity and or capital investment.
I’m responsible for deploying a holistic project risk management process. I develop process improvements, capture learnings, and on the people side, I’m also responsible for growing the risk management profession by developing competency and providing training.
How in your role did you come to be so interested in understanding the human side of failure?
I see this as the next step in the evolution of applied risk management principles in the oil and gas industry. It’s a personal area of research that involves understanding a linkage between safety incidents and barrier weaknesses — barriers meaning risk management barriers.
Our experts’ research into human performance deal with two of the three types of barriers we generally see: passive, active and procedural barriers. Passive systems barriers do not require human intervention. Active and procedural barriers do require human intervention, so it is in those two barrier groups where further research is warranted.
We hope to learn from these incidents and their relationship to weak barriers, so we can use risk management tools and principles to prevent future incidents.
What is human performance exactly in the context of the oil and gas industry?
And why is it so important right now?
Human performance is about understanding and improving how people interact with the plant, processes, and each other to create a safe state environment. In hazardous industries like oil and gas, it is unrealistic to believe we can be 100 per cent safe. The best we can aspire is to work in what we call a “safe state.” We need to understand incidents from the point of view of the person – which is the next step in the understanding of incidents.
In previous years, investigating incidents meant asking who was involved and who was at fault. Now, our experts’ believe we should shift our focus onto what happened and why. The end goal is to learn better, because we are not learning from incidents — evidently — because they keep occurring. Now is the time to get better at this.
Why is it better to ask what and not who in the investigation of safety incidents?
We can learn from human error by making “learning” the focus of the investigation, rather than assigning blame. We need to develop an approach specifically designed to understand the actions of humans in complex systems.
The first thing I think we have to accept is that human error will always be present anywhere there are humans. And that human error occurs because of something else beyond negligence, like focusing on a task, but overlooking the potential hazards associated with said task. Another key element of understanding human performance is looking at how we, as leaders, react to these incidents. How we respond as leaders is important because it determines how well we’re going to learn and prevent future incidents.
When leaders choose to listen and learn, people tend to be much more open and it builds a foundation of trust. Our experts believe that when another incident occurs in the future, those involved will be much more comfortable in having a dialogue with their leaders, which helps everyone better learn from the incident.
If we have leaders who work alongside their teams to solve problems, we create what is known within BP as a culture of care. We get to see the activity set from the worker’s point of view, and we begin to understand what can truly go wrong and how to prevent it.
What is BP currently doing in the field of human performance?
At BP, our human performance experts have developed a framework around human performance, and it includes the elements against which we will eventually measure ourselves and our performance.
First, we must acknowledge that people will make mistakes. That’s a fact.
With that in mind, we must realize that people’s actions are not inherently malicious. Those actions usually make sense to individuals leading up to and during the incident. With those acknowledgments in place, then we can evolve into understanding the underlying condition and systems that led to that incident, rather than assigning blame.
The way we behave as leaders in BP helps shape the conditions that influence what people do and how they do it. The Human Performance Framework continues to evolve as our experts’ research into the fields of health & safety, and risk management for further clues. What do the current learnings of our incidents tell us? How can we merge our safety rules with industry practices for better alignment, and thus expand our learning base? What can we learn from our project risk management efforts?
These are the questions we strive to answer soon. Our work in this space continues.
Hugo and more than 250 heads of Operations, EH&S, OE, ORM, and Maintenance & Reliability will be at the 2019 Operational Excellence in Energy, Chemicals & Resources Summit in Calgary, Alta. for three days packed with panels, case studies, workshops and peer-led roundtables on Process Optimization, Leadership & Culture, Asset Performance Optimization, Digital Transformation, Innovation Acceleration, Health & Safety Excellence and Operational Risk Management. The summit runs from June 4-6.
Print this page