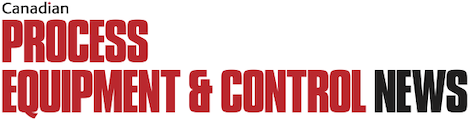
New work roll bearings significantly increase service life
Don Horne
Products ippt Level Products Mixing/Blending Separating SystemsNSK Ltd. has developed a four-row sealed tapered roller bearing with water resistant grease.
The tough environments found in steel mills require components that can withstand the challenging conditions as well as contribute to keeping cost and energy consumption down. New work roll bearings for rolling mills from NSK offer greater reliability and longer service life.
NSK work roll bearings are packed with a newly developed grease that extends service life even under severe conditions, including water inclusion. The new grease composition offers a thicker oil film and protective layer between the raceway and rollers.
Grease additives also inhibit corrosion which boosts the service life in conditions where water has potential to enter the bearing. Increased service life equates to reduced maintenance costs and increases operational efficiency. In addition, with reduction in need for replacement, CO2 emissions and resource consumption are also reduced.
In addition to contending with extreme environments, work roll bearings carry heavy loads at high speeds and temperatures while under constant exposure to water sprays and metal particles. These severe conditions can lead to premature bearing failure due to damage conditions such as flaking.
Flaking occurs when fatigue causes small pieces of bearing material to break away from the smooth surface of the bearing raceway, creating coarse regions within the bearing that can eventually make bearing inoperable.
Failures can also result from rust and water, used for cooling, entering the bearing and potentially causing seizure. In effort to increase reliability and ensure long service life, NSK has designed a special seal that helps to keep out water and other particles.
The newly designed sealed bearing offers two benefits. With an optimized internal design, an increase in load rating is achieved. Additionally, the improved seal design inhibits water from entering the bearing which can reduce contamination of the grease and improve bearing performance.
With these two significant improvements, real world test validated dramatic gains in bearing service life. For example, bearings in a specific mill are now achieving 16 months service life compared to conventional bearings typically lasting less than 8 months.
Product Benefits
Increased service life equates to higher operational reliability, fewer replacements and reduced downtime for repair. Longer service life also reduces material and energy consumption (including CO2 emissions) relative to the replacement cycles of conventional models.
www.nskamericas.com
Print this page