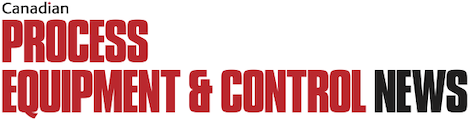
What Fixes the Problem with Portable Gas Detectors?
Installing fixed gas detection or using personal and portable instruments, to address facility toxic gas and flammable vapor hazards, is an important part of a comprehensive safety program. However, the objectives can be compromised by a lack of training, failure to adequately maintain products, misapplication, poor installation or equipment selection and a lack of complete knowledge of the hazard.
Gas detection product sales are comprised of ~45% portable products, ~10% detector tubes and ~45% fixed systems. Portable instrument sales have grown dramatically over the last 20 years as their capabilities and quality improved, prices moderated and the applications became better understood. In the 1990s, U.S. OSHA Confined Space Regulations most certainly accelerated development of improved instruments as well as fixed systems, which in many cases shared gas sensors with portables. Fixed systems costs have also moderated and products now have advanced sensors with universal transmitters, non-intrusive interfaces, data logging, optional alarms, wireless features, communication protocols, SIL ratings and Intrinsic Safety.
U.S. OSHA defines an area as confined space if you could be exposed to 10% LEL or greater, 19.5% Oxygen or lower or the TWA or a higher value of a toxic gas. While there are many other characteristics such as difficulty of egress that may make an area ‘permit required confined’ space, the designation nevertheless requires restriction and signage at a minimum and planned entry procedures with a rescue team at the maximum as required by law. Confined spaces are normally sampled prior to entry by using either a motorized pump or a hand aspirator. Considerable training is required to make a team efficient at this type of work and prepared for rescue.
Beyond confined space applications, which include sewers, a common portable application is for Hydrogen Sulfide detection. Persons carrying a portable H2S monitor usually have a respirator on their belt. But in locations where foot traffic is common, fixed H2S gas detection might be more economical and serve the purpose more effectively. The fixed installation protects people but also serves as process leak detection when no one is present. In this manner timely mitigation measures are taken and appropriate preventive maintenance can be scheduled.
Another frequent application is the personal Oxygen monitor. Extreme caution is urged here as this device cannot be used to enter a suspect area. By the time a portable gas detector responds to low Oxygen after a few seconds, the wearer will have taken a couple of breaths and be down on the floor. Such a place is better sampled before entering, or protected by fixed point gas detection with warning at the door if there is frequent use of the area.
Competent users of portable gas detection verify operation, prior to each use since they are usually shut off. The recommended steps are to verify the battery charge level, zero the sensors in clean air and finally bump test the gas sensors. Fixed systems are always powered on and therefore have a regular PM schedule consisting of calibration (monthly to annual) with perhaps bump testing between calibrations. Certain sensors always fail safe to fault/alarm (Oxygen and Infrared) but others can fail and not alarm and so a bump test or calibration is the only way to determine if the sensor is functional.
Catalytic bead combustible sensors can be inhibited or poisoned and toxic sensors simply fail to respond. In fixed systems, a ‘percent remaining life’ function is extremely useful as is continuous diagnostics and a test-on-demand or ToD cell which can bump test toxic sensors manually or automatically at predetermined intervals.
Choose gas detection products carefully. Fixed systems perform most applications very well indeed but must be installed in the facility and meet the area hazardous classification, if any, as well as provide adequate warning and annunciation. On the other hand, portables need charging stations, much more frequent checks and maintenance plus good record keeping. Portables also have a 10% to 20% loss ratio. Always purchase listed products, that is, those tested and approved by a third party (CSA, FM, UL, et al) to meet the area electrical classification and approved (listed) for the intended application.
While one automatically selects a sampling portable for confined space, the default product selection for process leak detection and many other applications is fixed systems. Many codes, regulations and standards call out fixed gas detection for specific circumstances. These include but are not limited to flammable liquid storage, waste treatment, solvent extraction, dry cleaning, battery and gas metering rooms, compressed gas cylinder storage, aerosol filling, fuels handling, Hydrogen systems, CNG and LNG systems, foam manufacturing, transportation terminals and parking garages, LPG terminals, refrigeration, flame/smoke audience effects, landfills and recycling, tunnels, potable water disinfection, plating, welding, plasma spraying, and many other commercial, manufacturing and industrial processes.
Consult your gas detection suppliers and provide them with complete information to develop a suitable solution for your gas monitoring needs. Remember, they have a lot of valuable information and experience to share with you. Lastly, keep in mind that portable gas detection protects people, whereas fixed gas detection provides process leak detection and loss prevention as well as protecting local personnel.
Stephen G. Phelps is the Applications Engineering Manager for Sensidyne and a graduate of the Rochester Institute of Technology. Steve has over 35 years experience engineering gas detection systems for safety applications and currently works closely with the Sensidyne Sales Channel Partners and customers to solve challenging applications.
Print this page